South Australian men's sheds give new life to waste material while offering social benefit
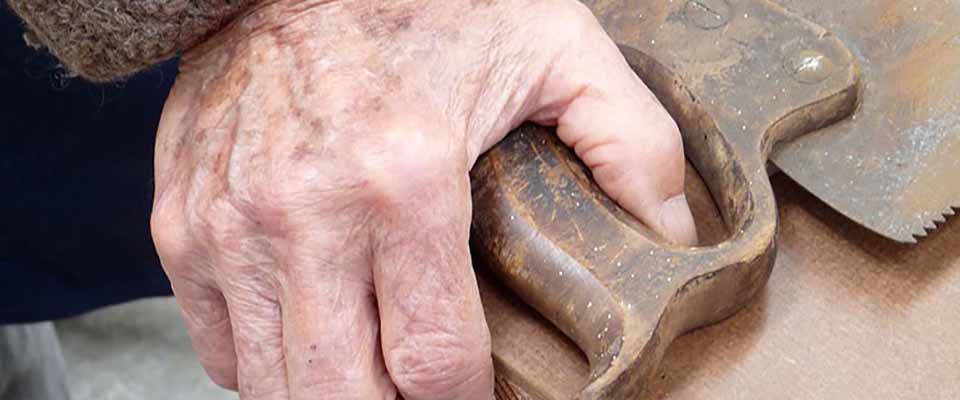
Men's sheds pass on skills in recycling, repairing and refabricating waste materials.
Image courtesy Australian Men's Shed Association
The network of men’s sheds, with 13 in the Adelaide metropolitan area and 70 in the regions, received South Australian government support its activities in turning waste into resources, and extending the life of items through reuse, remanufacture and repair.
The Mount Pleasant Men’s Shed's Complete the Circle project was an example of those receiving grants under Green Industries SA shared fabrication spaces infrastructure programme.
The $27,850 grant funded the shed’s work on source waste materials from the local area then rework these resources into saleable and donated products. Recycling and repurposing a local waste stream contribute revenue for the shed and builds a shared hub of tools and equipment where shed members learn new skills, and practise and pass on skills in recycling, repairing and refabricating.
South Australian surveys show that timber and wood is 8% of waste disposed to landfill by weight. Kerbside collection services don’t capture 44% of timber and wood waste. Sheds, such as Mount Pleasant, target this stream.
Since 2012, members have raised $130,000 to build the shed, with Barossa Council giving a 21-year lease of public land to build the shed, along with a $32,000 grant towards the project. Shed volunteers collect waste timber from businesses and groups or from buildings. Damaged or discarded items from waste transfer stations also can be salvaged, repaired and restored. Shed members also have repaired structures, recycling building materials, removed fallen timber, repurposing trade waste from businesses and done restorations after bushfires.
It runs workshops in ideas using wood and building waste, including new flat-pack products such as palette furniture and planter boxes.
The South Australian Men’s Shed Association has information on the locations of the sheds that also offer the mental health benefit of social activity.